13Mari: Success Story
Navigating toward reduced fuel costs and cleaner waters
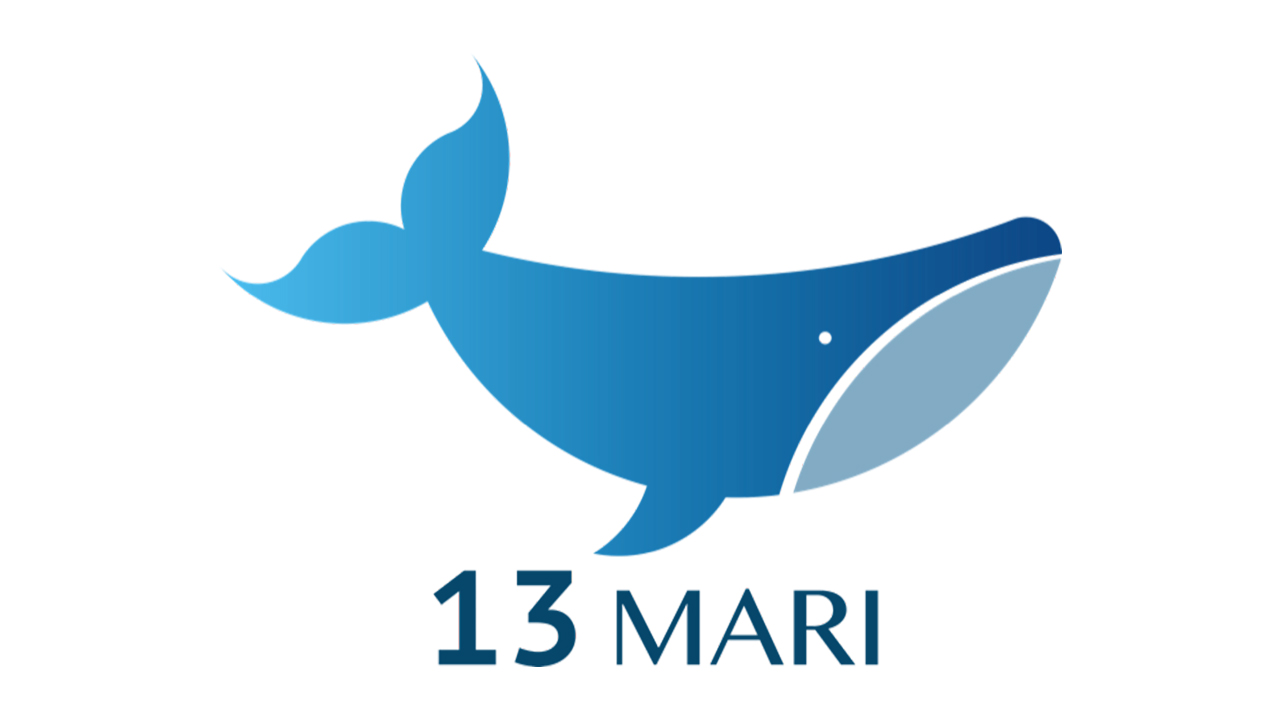
Fuel costs are top of mind these days as we fill our tanks at the pump. But imagine how expensive it is to fill the tank of a commercial maritime vessel.
Container ships, cargo ships, bulk carriers, and oil tankers require fuel for internal workings and the obvious — traveling across bodies of water for thousands of miles. Fuel costs are the number one expense in the international shipping industry. They represent as much as 50-75% of total ship operating costs, and prices continue to soar. Ship & Bunker reports that shipping fuel costs have risen over 40%, and as of this writing, the price of VLSFO (very low sulfur fuel oil) stands at 975.5 U.S. dollars per metric ton.
Then there’s the matter of emissions to consider. The International Maritime Organization (IMO) has adopted mandatory measures to reduce emissions of greenhouse gases from international shipping. They’ve established the pollution prevention treaty (MARPOL), the Energy Efficiency Design Index (EEDI) mandatory for new ships, and the Ship Energy Efficiency Management Plan (SEEMP).
How can the maritime industry further reduce fuel costs and create cleaner waters? 13Mari is building a solution.
13Mari, where green meets blue
The company has developed a simple, elegant approach to fuel efficiency with a composite element designed to reduce “drag.” Drag is precisely what it sounds like — the resistance created by shipping vessels moving through water. The larger the ship, the greater the drag, and the more fuel the ship uses.
By installing 15-30 of the 13Mari elements to a ship’s hull, without compromising it, ship owners could reduce drag by up to 7%. That translates to fuel savings of 7% and a reduction in operating expenses of 3-5%. Higher fuel prices now make up 50-75% of operating costs and continue to rise. While only a portion of the hull can be effectively covered at this stage, 13Mari anticipates a drag reduction of up to 20% in the future – the drag reduction a single element exhibits. 13Mari estimates that using their product in MVP state can eliminate 45,000,000 tons of CO2 (carbon dioxide) per year.
FORGE makes connections
13Mari’s component had the potential to make an impact from both a business and sustainability perspective. Finding a means to test and validate the physical element strength and installation protocol was the logical next step. The question for 13Mari was, “How do we find a quality control partner?”
Enter FORGE. Knowing the strengths and focus areas of their network enabled the FORGE team to make several introductions to quality control partners, which saved 13Mari valuable time in validating their product. As Krassi Fotev, co-founder of 13Mari, explains:
“The direction we’ve gained by working with FORGE has been amazing. FORGE has accelerated the process for us by coming up with a list of compulsory specialists with lab capabilities — three to five introductions — in a shorter amount of time than we ever could have on our own. In days, we were having conversations that would have taken us months to cultivate.”
13Mari chose to work with Intertek, an industry leader in total quality assurance with a deep understanding of maritime technology. 13Mari connected with Intertek’s composite specialists to perfect the element’s design and address detachment concerns, which accelerated progress. As Krassi explains, “Intertek’s composite specialist came up with a solution in a matter of minutes, and we continue to work with him on design and installation protocols.”
What’s on the horizon for 13Mari
FORGE connects fast-growth companies to manufacturing partners who continue to work together in long-term, mutually beneficial partnerships.
In 13Mari’s case, they’ve found a true collaborative partner in Intertek. While validation testing continues, Intertek has facilitated better communications among 13Mari and their investors. This connection has enabled 13Mari to keep investors updated on progress and provide assurances on design and installation.
The investment of time and resources now positions the company to scale with minimal re-design of the element while optimizing the installation process.
From 13Mari’s perspective, FORGE’s introduction helped the company navigate the maritime industry, a new area for them. As Krassi explains, “My education is in physics, and most of my professional life has been in information technology. Interestingly, my physics education helped me make the observation that helped people in the maritime industry. Getting to a lab with the resources for testing execution is not an easy process for someone outside of the industry. FORGE was instrumental in helping us overcome that hurdle.”