Active Surfaces: making solar power more flexible
Lightweight, durable solar panels flex and bend to generate power from more surfaces
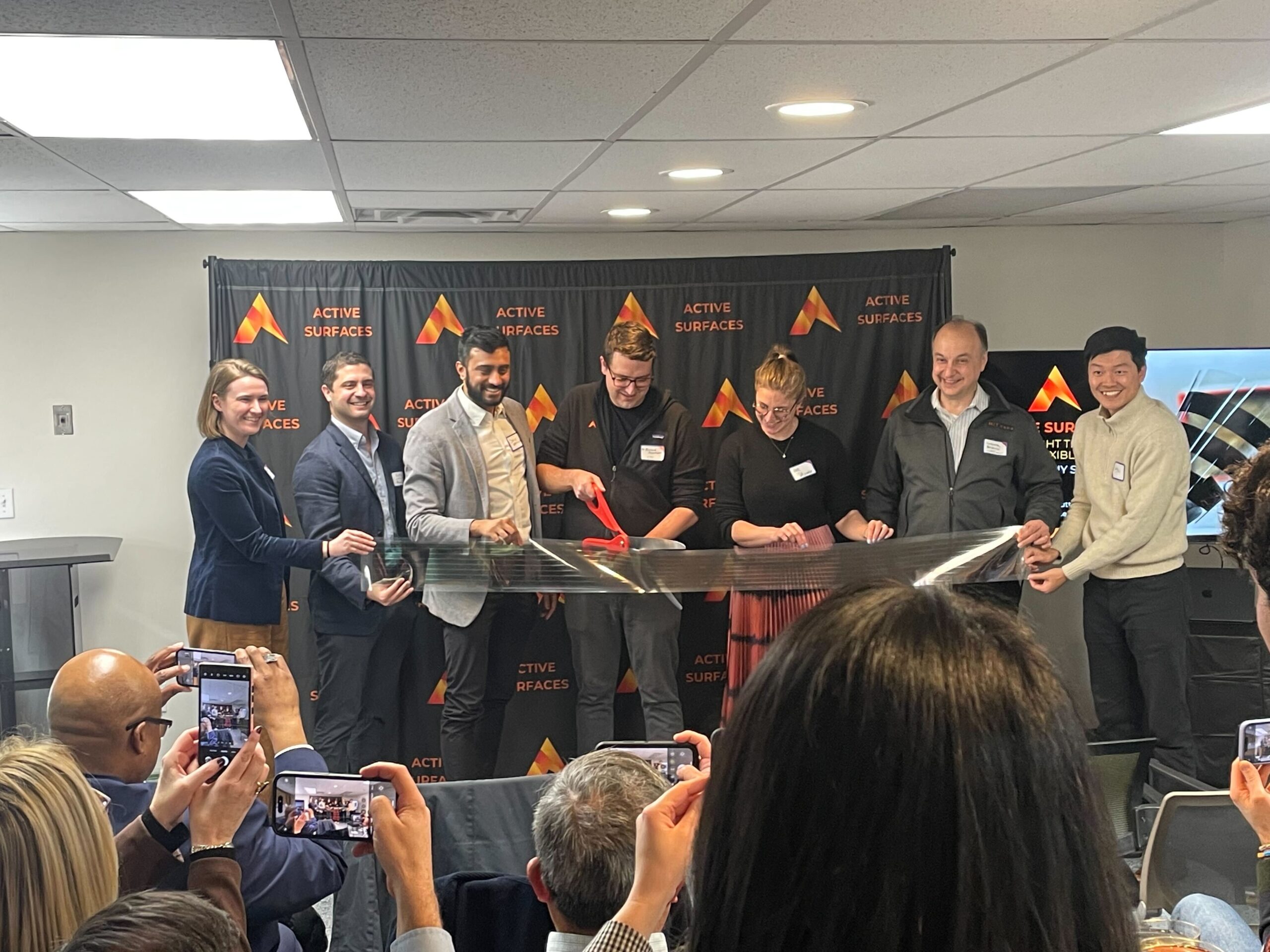
To meet humanity’s growing energy needs without increasing emissions, we need to deploy far more renewable electricity sources like solar power. We can use traditional silicon-and-glass solar panels in solar farms and on some roofs, but those don’t work for every application. Luckily, two MIT-educated entrepreneurs, the co-founders of Active Surfaces, have added a new type of solar module to our options. This module is flexible, lightweight, and easy to deploy on a wider range of surfaces.
From bench research to manufacturing research facility
Active Surfaces’ technology originated from Dr. Richard Swartwout’s PhD work at MIT. With a PhD in Electrical and Electronics Engineering focused on solar and printed electronics, he had been working on flexible solar panels since 2015.
Dr. Swartwout and Shiv Bhakta met in class while Bhakta was studying for a combined MS/MBA through MIT’s Leaders for Global Operations. The two joined forces to work on the solar panels. After their pitch for the product won first place at the MIT 100K and Harvard Climate Symposium, they officially launched their startup, Active Surfaces, in 2022. The name ‘Active Surfaces’ comes from the company’s vision: to activate every possible surface with solar power.
“It’s akin to a solar yoga mat that you can unroll and stick onto almost any surface, from the sides of buildings, rooftops, the tops of cars, satellites, and IoT devices,” Bhakta said. “We’re able to manufacture it locally with a new approach. We use roll-to-roll manufacturing – something Massachussetts is known for – to make something with competitive performance and lower costs than traditional solar panels.”
A traditional solar panel typically weighs 50 pounds. To generate a megawatt on the rooftop of one commercial or industrial building, you’d need 2,000 panels. That’s 50 tons of solar panels! Most buildings couldn’t handle that much weight without costly structural reinforcement. With Active Surfaces’ solar modules, which are more than 90 percent lighter, the same number of panels would weigh less than 5 tons.
Active Surfaces’ product has drawn attention and funding, helping the startup grow. In just two years, Active Surfaces has gone from an MIT lab spinoff to an innovative company with its own small-scale manufacturing facility.
Scaling up, locally, with FORGE
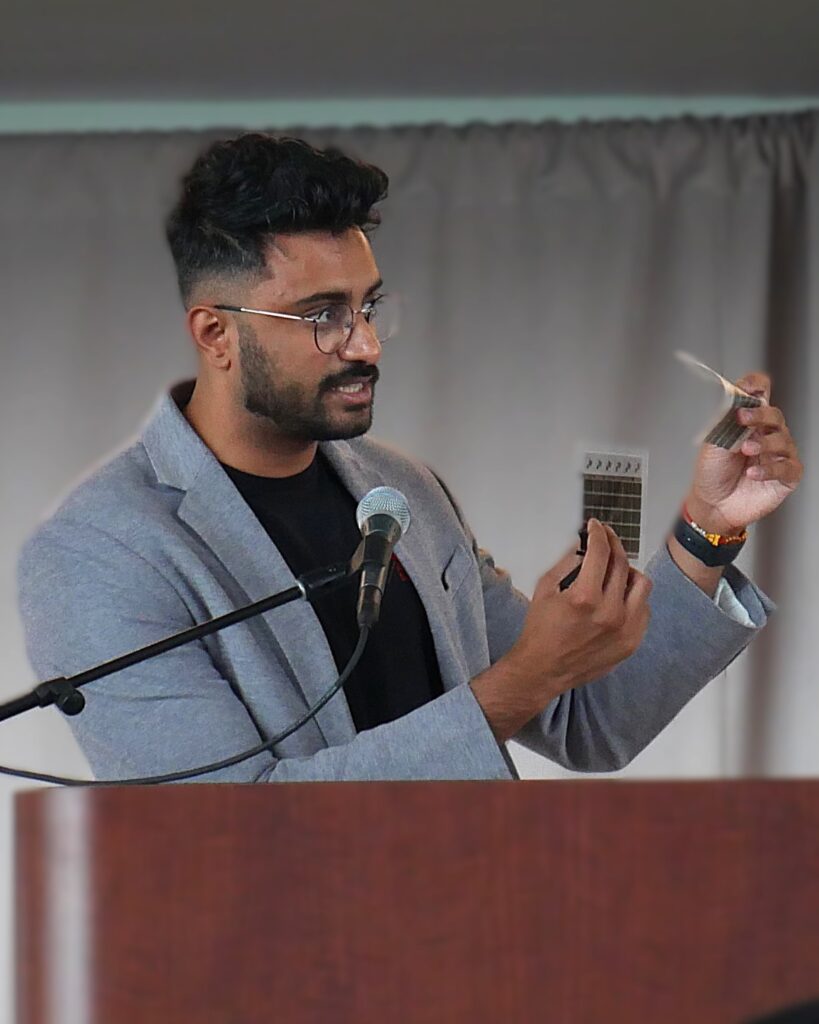
Active Surfaces just opened a 4,800 square foot manufacturing facility in Woburn, MA. There, the company can do small-scale production, R&D, and demonstrations for customers. The building is part of FORGE partner Cummings Properties’ innovation cluster.
Many steps led to this big milestone. To justify opening a facility, Active Surfaces needed commercial demand, to successfully file its IP, and to create a prototype large enough to get investors interested.
FORGE has contributed to Active Surfaces’ journey to scale. Bhakta and Swartwout first learned about it through Greentown Labs’ ACCEL program. They applied to FORGE’s cleantech pitch competition at the 2024 Massachusetts Manufacturing Mash-Up. Their pitch won second place and a $6,000 non-dilutive FORGE Product Development Grant.
Active Surfaces used the grant to partially fund equipment for an outdoor pilot on a local coworking space’s rooftop. The pilot pitted the solar modules against their real-world use case, showing that Active Surfaces’ system and adhesives could perform.
“The grant we won from FORGE was helpful,” Bhakta said. “The use of funds was entirely on product development, so we can show customers a larger prototype that actually works, validate it from a testing perspective, and make something as close to the final product as possible. We plan to leverage FORGE more as we focus on scaling our product and more and more on manufacturing.”
Active Surfaces plans to consult with FORGE and members of our supply chain network for mentorship around roll-to-roll manufacturing at larger volumes, and to source materials and manufacturing locally.
“Over 95 percent of the solar supply chain is in China today,” Bhakta said. “You’re forced to manufacture closer to where you get your materials. We can get materials for our product near Massachusetts and manufacture it locally, something that was never possible before.”
Looking forward: rapidly scaling to meet solar deployment goals
Active Surfaces has big plans going forward. The startup will do more outdoor demonstrations of its solar modules with commercial partners and validate that a flexible solar panel is interesting to the world and solar market, especially with commercial and industrial customers. Active Surfaces will continue to grow its manufacturing capabilities, team, and knowledge to deploy meaningful numbers of solar panels in the next three to four years.
Bhakta’s hope is to help accelerate the deployment of solar power to meet net zero carbon goals. To meet net zero, he says humanity needs to deploy 20 to 100 times more solar power. That’s a tall order. And that’s why expanding solar power generation to more surfaces with flexible solar panels can make such a difference.
“Active Surfaces isn’t trying to replace traditional solar panels,” Bhakta said. “Instead, we’re adding solar in places traditional solar can’t go.”
We’ve always known that making our energy sources fully renewable would require adaptation and flexibility – but we didn’t realize physical flexibility would make such a difference. We look forward to seeing Active Surfaces on more surfaces around us soon!
By the numbers
- Active Surfaces’ solar module is more than 10 times lighter than a traditional solar panel
- The installation cost of Active Surfaces’ product is 70 percent lower than traditional solar