Atacama Biomaterials: Success Story
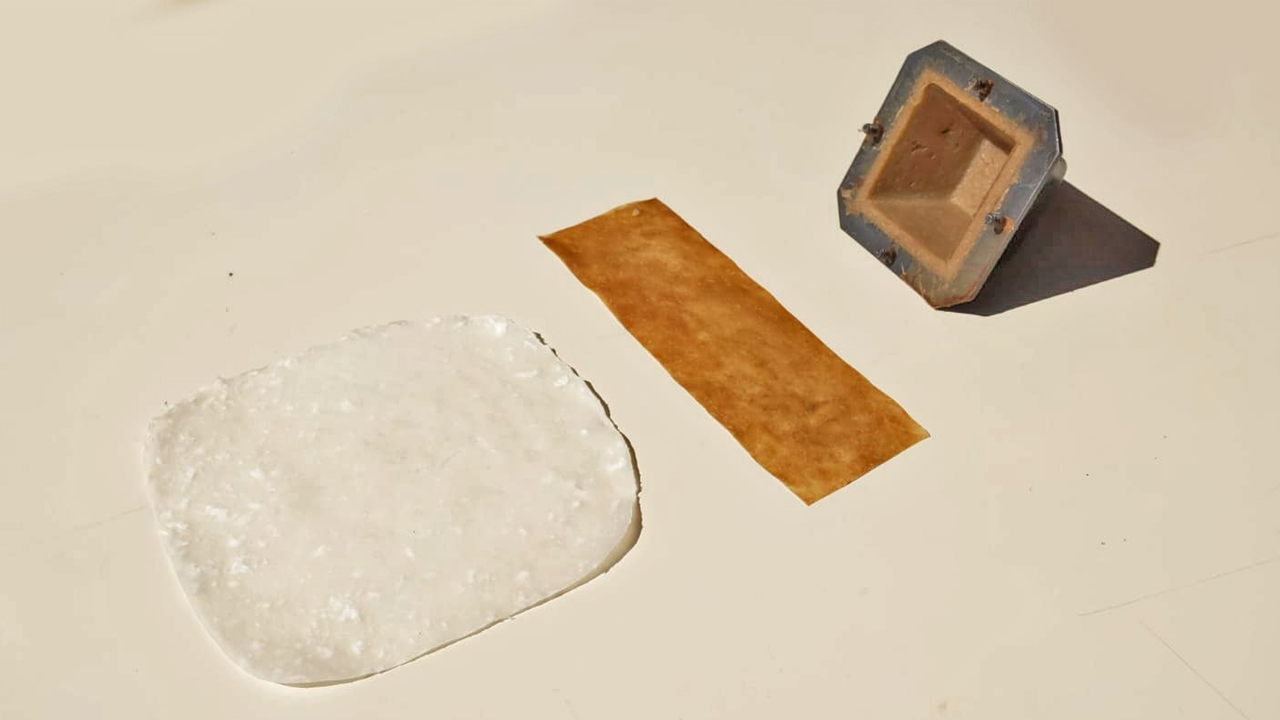
Recipient of the FORGE Product Development Grant, disrupting packaging with robotics and AI
Creating a sustainable substitute for plastic film
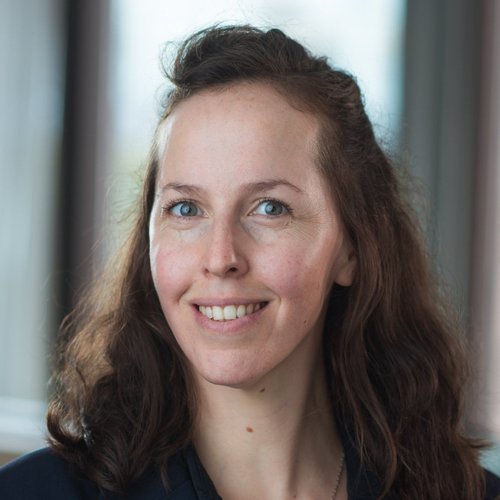
While Dr. Paloma Gonzalez-Rojas was working on her Ph.D. in machine learning at MIT, she couldn’t stop thinking about climate change. She wanted to make renewable polymers, but it didn’t fit into her degree’s research focus. So she started a side project.
Gonzalez met her co-founders in a 3DEXPERIENCE Lab in Waltham, MA. She, Jose Tomas Dominguez, and Jose Antonio Gonzalez launched a biomaterials startup. They named it after the Atacama Desert in their country of origin, Chile, symbolizing their desire to keep plastic from harming the environment.
“As Chileans, we know what goes to the desert, stays in the desert, so we can find all sorts of waste and debris there. We don’t want that to be the future of one of our beloved places,” Gonzalez-Rojas said.
Inspired by Gonzalez-Rojas’ postdoc research on AI and Dominguez’ work on solar panel maintenance robots, Atacama shifted the focus to packaging materials and designed Woodpack. The compostable wood-fiber film replaces single-use flexible plastic films like garment packaging and grocery bags.
“Paper bags and plastic bags both have major drawbacks – we have something that’s better,” Dominguez said.
The founders’ high-tech skillsets helped them develop this unique solution. Gonzalez-Rojas found an algorithm to identify variability in materials and make Woodpack more consistent.
“We aren’t just using AI and robotics because they’re fun,” Gonzalez-Rojas said. “Cleantech, to me, means hope for the future. It means we’re going to save the earth.”
FORGE’s impact
Gonzalez-Rojas found out about FORGE’s product development grant through a friend. The team was excited to see a grant focused on cleantech startups with historically marginalized leadership. They’d been seeing news that investment in Latin entrepreneurs and women was trending downward.
“We were scared it wasn’t the right time for us, even if it was the right time for our idea,” Dominguez said. “We’re really thankful to FORGE for building up the ecosystem for minority founders.”
“We really wanted to apply for FORGE’s grant,” Gonzalez-Rojas said. “We have to work so hard to prove ourselves. It was important to us to be part of this community that understands that bias.”
FORGE’s grant is funding a pneumatic gantry system, a major component for the alpha prototype of Atacama’s robot. They’ve been testing each stage of the manufacturing process manually in the lab, but now they need to make each stage scalable and automated. The gantry system, which dries the material, makes up about 40 percent of the robot.
“The support from FORGE is fundamental. It’s almost half of the robot,” Gonzalez-Rojas said.
Looking ahead: Woodpack goes commercial
Atacama is seeking angel investors and getting ready to raise seed funding by mid 2023. Woodpack production is advancing from proof-of-concept to alpha prototype. Atacama is making Woodpack at a lab scale to bring to potential clients for feedback. They want to make Woodpack producible at a massive scale.
“We’ve been very lucky to bootstrap through MIT and other resources, but next year we want to start running,” Gonzales-Rojas said.
Atacama’s first clients will be e-commerce garment retailers. Consumer demand for green packaging is growing, so Dominguez thinks retailers will jump at the opportunity to replace poly bags with ones made of Woodpack.
Atacama is targeting companies that use smaller amounts of plastic film first. As their manufacturing robots grow in capacity, they’ll start selling Woodpack to construction companies to replace products like plastic sheeting. But construction and e-commerce are just the beginning.
“We want everyone to use it,” Gonzales-Roja said. “Every single-use and disposable plastic – we want it to be us.”
By the numbers
- Atacama holds 4 patents
- Only 7 percent of all plastic packaging is recycled. Woodpack is the only bioplastic made of recycled paper, and is itself compostable
- Atacama reduced the time it takes to produce Woodpack by 99 percent between lab tests and proof-of-concept production
- Woodpack has a 70-75 percent lower carbon footprint than PLA and LDPE plastics. If it fully replaces plastics in flexible film, Woodpack will eliminate 2.5 gigatons of CO2 emissions per year by 2030
- If Atacama can build materials to replace other forms of plastic packaging, they could eliminate 140 million tons of plastic waste a year