Locally grown startup prevents food waste with cold plasma
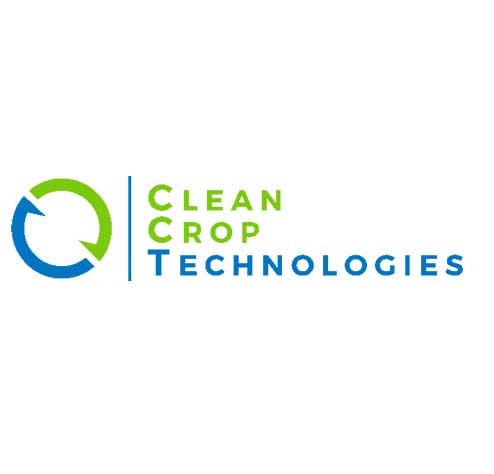
Holyoke-based companies build futuristic tech to safely nix food contaminants
At FORGE, we love expanding local supply chains to support the innovation ecosystem, so the story of how we introduced Clean Crop Technologies (Clean Crop) and Cofab Design is one of our favorites!
Clean Crop is an agtech company using electricity to boost crop yields, reduce food waste, and improve food safety. Cofab Design is a mechanical product development studio that brings the creative energy of a design studio to the technology development and manufacturing world. Since teaming up through a FORGE connection, the two companies now share a building in Holyoke, collaborating from one floor apart.
From lost peanuts to cold plasma
Dan White, CEO and co-founder of Clean Crop, was working in sub-Saharan African agricultural supply chains when he met COO and co-founder Daniel Cavanaugh.
“Every day, we confronted food supply chain issues,” White said. “For each step from farm to fork, contaminants like salmonella and mold spoil food. By the end, 30 percent is lost. It’s a massive cost driver for food supply chains, and an overall problem in the world that has yet to be solved.”
Constantly losing peanuts to aflatoxin at a shelling operation drove White and Cavanaugh to seek a solution. That’s how they met Dr. Kevin Keener, a professor at Iowa State University. Dr. Keener was a leading expert in a high-voltage cold plasma technology, which looked like a viable solution to address the chronic issues plaguing global food supply chains. On their return to the U.S., they began experiments with what would become the firm’s proprietary Clean Current technology, which combines food-grade gasses and electricity to remove contaminants without compromising quality.
Clean Crop moved into a space at the UMass Amherst Institute for Applied Life Sciences (IALS) and also leased an industrial space in Williamsburg, MA.
White, Cavanaugh and Keener co-founded Clean Crop to commercialize Clean Current technology and apply it to the world’s food supply chains. They leased an industrial space in Williamsburg, Mass. and began gathering data and building their first prototype.
Making the Holyoke connection through FORGE
In 2019, Clean Crop was ready to raise its first round of capital to grow its early-stage prototypes into a product ready for production pilots with partners around the globe. At a FORGE event, White met FORGE’s executive director, Laura Teicher. She invited him to present at another event in Springfield. There, he met Cofab partner Mike Stone.
White quickly saw the value FORGE could offer. He said, “FORGE helped us understand the hardware manufacturing ecosystem, as well as how to think about stages, resourcing, time and money as we put together a business plan. Their advice helped inform our capital strategy in the seed round.”
FORGE introduced Clean Crop to ecosystem collaborator MassChallenge, who helped Clean Crop secure a $2.75 million seed round. Clean Crop reconnected with Cofab in 2020 to use some of the funding for prototype development.
Stone said, “To stop chasing build problems and start refining their product, Clean Crop needed more sophisticated machines. We started collaborating and have gone through three or four pushes of work together.”
Stone joined the FORGE network in 2015 and later our Western Mass. advisory council because he valued our nonprofit format. The constant stream of FORGE leads has deepened the love. “FORGE provides value for us and the leads,” he said.
Clean Crop’s collaboration with Cofab enabled Clean Crop to bring a prototype to a pilot in Georgia in advance of their Series A fundraise. Soon, Clean Crop outgrew its workspaces in Williamsburg and at UMass.
Dr. Peter Reinhart, director of IALS and a clinical professor at the UMass Amherst Life Science Laboratories, said “We are proud that Clean Crop Technologies has achieved so much since their stay in a company Start-Up space in the Institute for Applied Life Sciences Collaboratories. This is exactly the sort of success story we envisioned when we dedicated high-quality space to startups in close proximity to our industry-friendly equipment facilities. They were also able to take advantage of the Massachusetts Innovation Voucher Program to access equipment at a significantly reduced rate.”
Now ready to scale up their operations, the Clean Crop team decided to move to Holyoke, in large part because the building Cofab was located in had an opening.
“Mike invited us to come look at the space in Holyoke. It ticked all the boxes,” White said.
The affordable, flexible space and local manufacturing ecosystem were a great fit. Clean Crop moved in. White said, “Being able to source parts from local machine shops with high tolerances and complex machining abilities has been a game-changer.”
But the best part was the convenience of having a collaborator one flight of stairs away.
“Having them upstairs is great for both of us and the growing inertia in Holyoke. We love having a cool neighbor building groundbreaking technology,” Stone said.
Looking forward: growing Holyoke’s innovation ecosystem, greening agricultural supply chains
Clean Crop has advanced to the late prototype phase and is beginning to commercialize. The company is working with FORGE manufacturing expert in residence Scott Longley to land additional funding and has issued a request for proposal to get its product into production. Longley is introducing Clean Crop to manufacturers.
“We’re going to be evolving over the next few years to build, support and operate these machines across the country and world,” White said. He’s excited to be part of a growing movement to electrify agriculture and liberate it from petroleum-based fuels and persistent chemicals.
Cofab is growing too, while maintaining its consultancy model and manufacturing specialization. Its relationship with Clean Crop is helping it show other startups the value of working in Holyoke and the greater Western Mass. innovation ecosystem.
“Companies like Clean Crop derisk by relying on a competent community, including partners like Cofab, readily available local contractors and even coffee shops, all of which keep their teams working on groundbreaking technology humming along,” Stone said. He hopes Clean Crop’s success will attract similar companies to Holyoke to take advantage of the city’s flexible real estate, uniquely affordable electrical utility and location at the crossroads of 91 and 90.
“More cool clients to team up with!” Stone said. “With planning and recruitment, we could create a decades-long wave of hardtech investment and growth in this city. It’s a once-in-a-lifetime opportunity for a place like Holyoke.”
By the Numbers
- Toxins, pathogens, molds and pests damage 30 percent of all food every year, resulting in $1 trillion in lost revenue, 600 billion cases of foodborne illness and 500,000 deaths. Clean Crop’s technology can degrade 83 percent of toxins and 99 percent of molds
- A third-party climate impact nonprofit estimated that, at scale, Clean Crop will offset a gigaton of emissions by 2050
- Cofab has received nearly 100 leads from FORGE, resulting in at least $500,000 in contract value
- Clean Crop has contributed more than $640,000 to the Western Mass. economy by tapping local vendors for leasehold improvements, machinery & equipment, R&D and other operational expenditures
- Clean Crop’s $100,000 Mass. state-level grant contributed to the company receiving more than $14 million in venture capital investments, a more than 100-fold return on investment